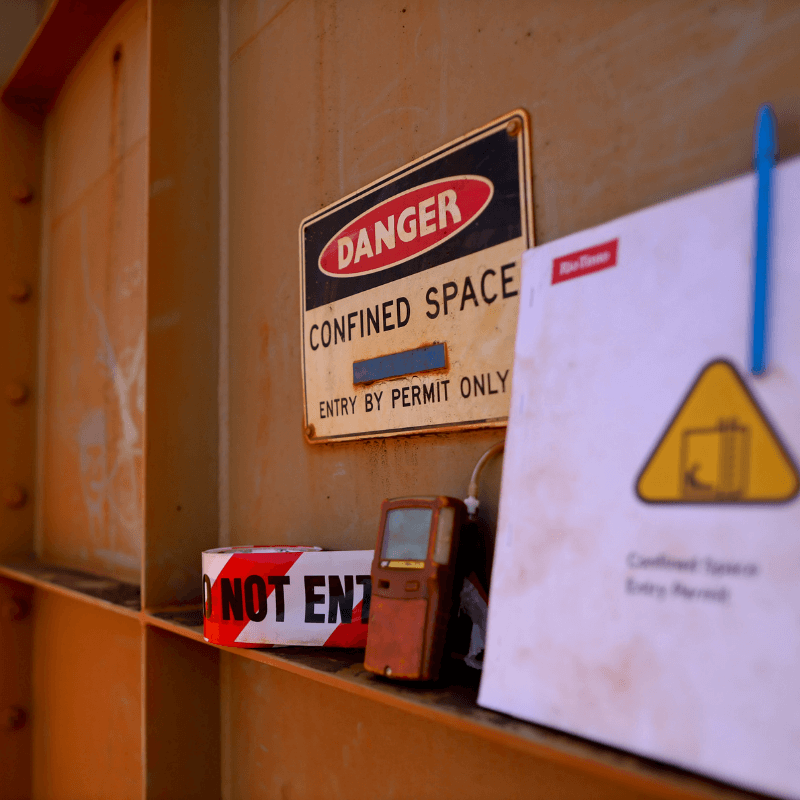
Updated on • 17 Sep 2024
Why Use Drones For Confined Space Inspection?
Drones are a key tool for indoor and confined space inspection, saving time, cutting costs, improving safety, providing accurate data, and reducing asset downtime. In-depth report, including case studies. ... Read More
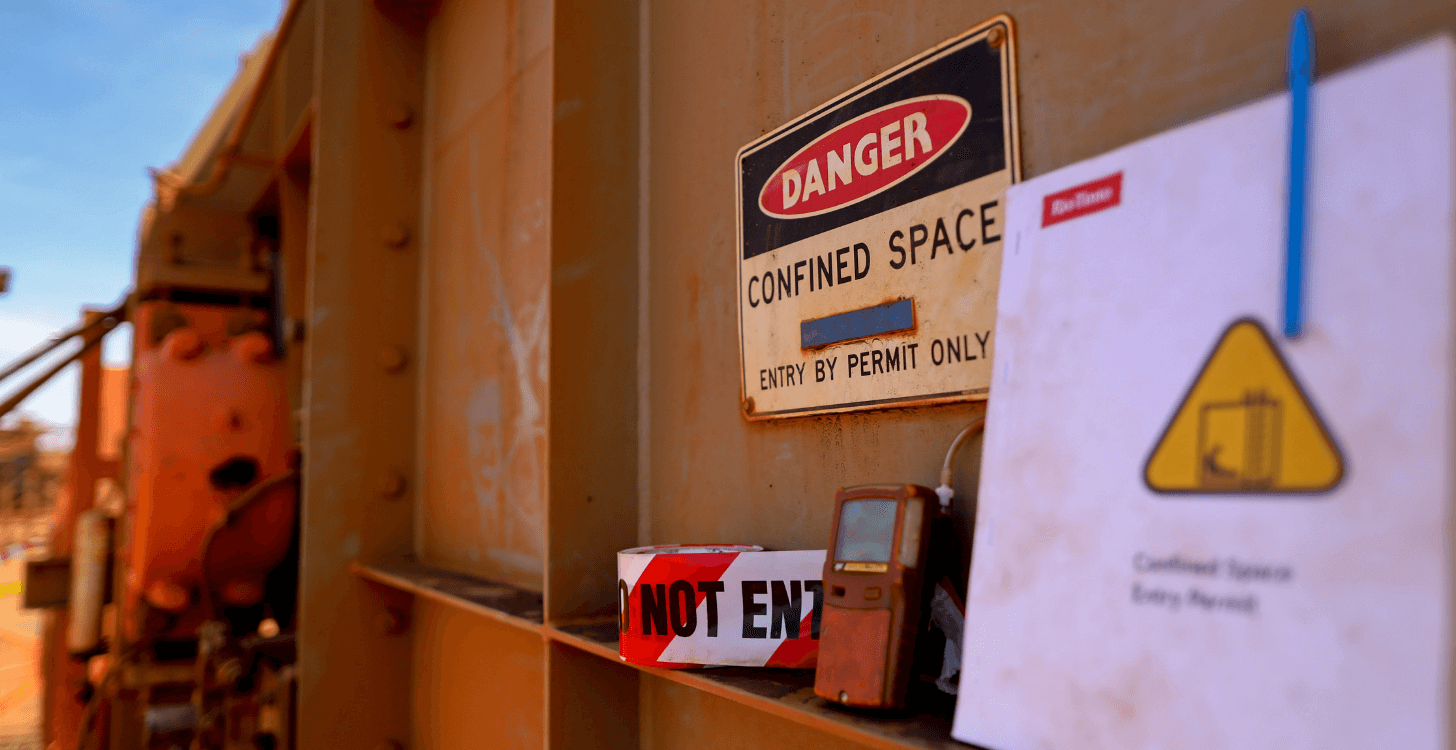
**Drones are a key solution for indoor and confined space inspection, providing remote access which enables cost savings, the collection of more accurate and repeatable data, and improved safety;**
Traditional methods - including manual inspection via rope access or scaffolding - can be dangerous, time-consuming, and labour-intensive, with prolonged periods of asset downtime;
In one example, it took 60 days to inspect 20 tanks with traditional methods; drones took just nine days - dramatically cutting asset inactivity, slashing costs and removing the need for risky manual inspection;
heliguy™ has designed a collision-proof cage for the DJI Mavic 2 Series, to offer 360° protection during confined space and indoor inspections.
Dangerous. Expensive. Time-consuming. Confined space inspection has traditionally been a risky and laborious task.
But a solution has emerged to alleviate these problems: Drones.
Unmanned aircraft are providing a reliable solution for inspecting hard-to-reach spaces, cutting costs by more than 80%, significantly reducing - or even eliminating - asset immobilisation, and improving on-site safety by removing the need for manned entry.
Drones have become an important remote visual inspection (RVI) tool, providing full visual access to highly-complex, hazardous spaces, especially when eyes-on human inspection is expensive, risky, and time-consuming.
Traditional Method | Drone Inspection | |
Data Quality | Low | High |
Risk To Staff | High | Low |
Speed of Inspection | Low | High |
Cost | High | Low |
Manpower | High | Low |
Asset Downtime | High | Low |
And to protect your aircraft against bumps and scrapes in confined areas, heliguy™ has designed a collision-proof Mavic 2 drone cage.
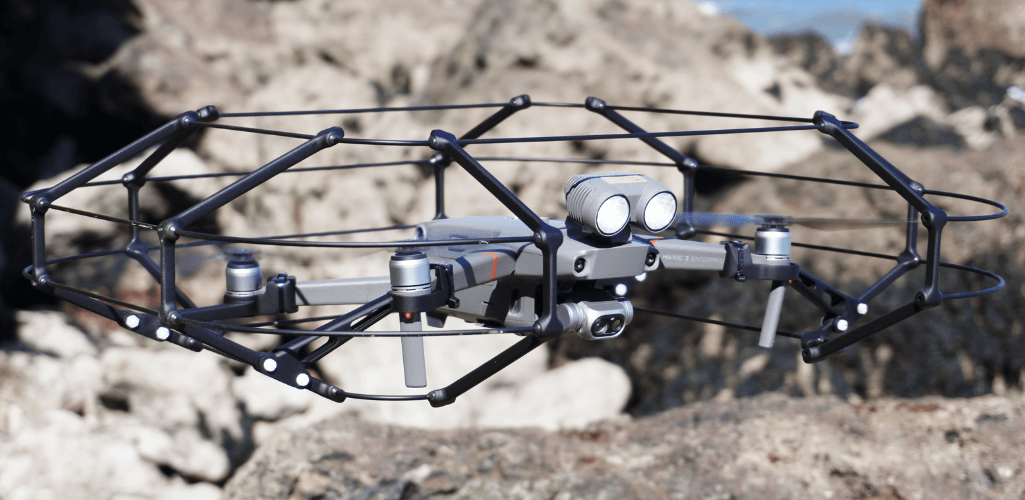
This blog will take an in-depth look at drones for confined space inspection and the benefits of deploying a drone cage for this type of work.
What Is A Confined Space Inspection?
Confined space inspection involves checking an enclosed or partially enclosed asset with limited means of entry.
This type of inspection is present in most industries, such as oil and gas, mining, construction, chemical, maritime, infrastructure (such as bridges), and waste-water and sewerage treatment.
Chimneys, flues, pressure valves, culverts, tunnels, ballast tanks, piping, boilers and silos are all require inspection.
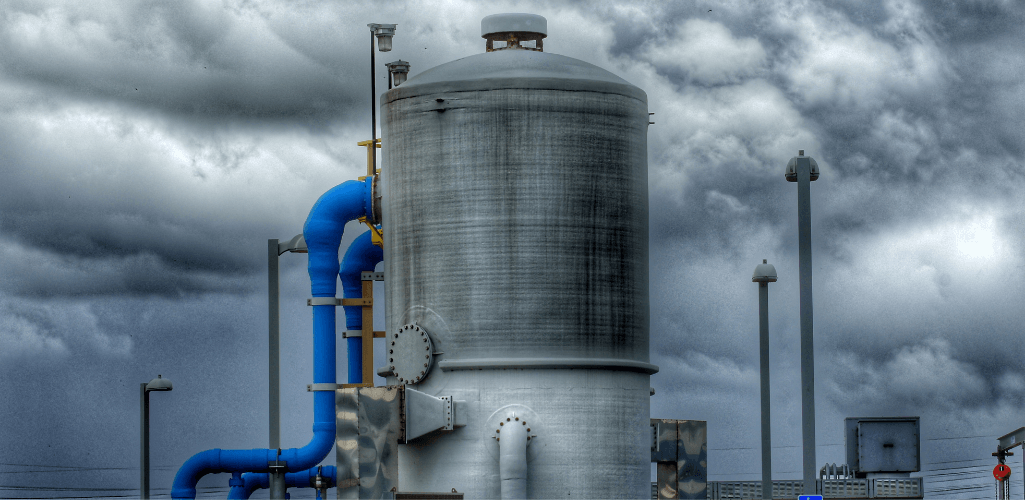
But, manually checking these types of asset present numerous challenges and limitations, and many companies are turning to drones for inspection tasks which would be performed by humans previously.
What Are The Problems Of A Traditional Confined Space Inspection?
Traditional methods of inspecting a confined space have numerous disadvantages and problems. These are mainly centered on three things: Time, cost, and safety.
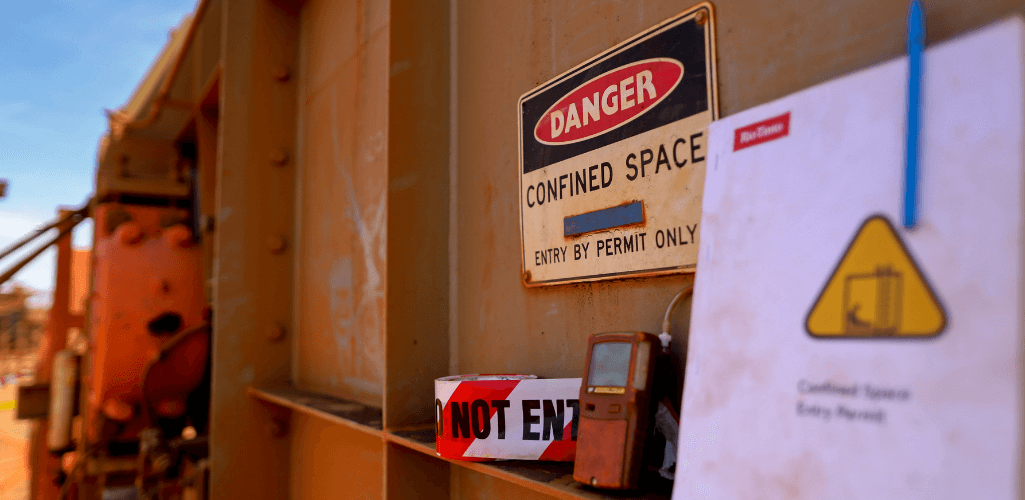
High Risk
Confined space inspection is a high-risk task, often taking place in dangerous and potentially volatile environments. In some cases, it can be fatal.
Asphyxiation is the leading cause of death from manual confined space inspection, caused by oxygen deficiency or exposure to toxic atmospheres.
Then there's other hazards, such as falling debris, entanglement, being hit by moving machinery, falling from height, and engulfment.
Accessing The Space
Traditional methods of inspecting confined spaces can be time-consuming, labour-intensive and costly.
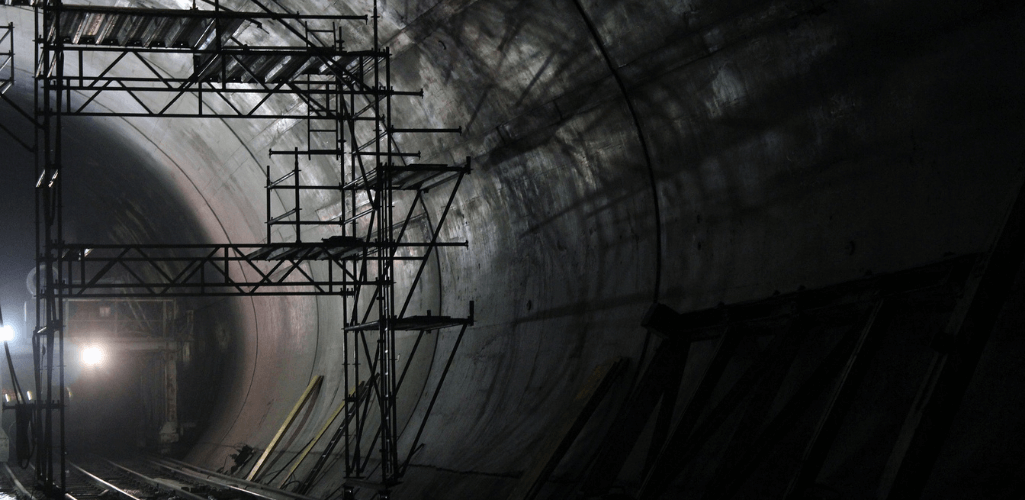
Part of this reason is the huge logistical implications of reaching the space - whether that be via rope access or building and subsequently clambering up and down scaffolding, which is costly, dangerous, and lengthy.
And once your team has eyes-on the asset, the data collection can be slow going and lacking quality.
Then there's the rigmarole of completing administration, and the high cost of purchasing protective equipment for certain jobs and the large number of specialist staff required to make the job possible.
Asset Downtime
Manual inspections are generally time-consuming affairs, and require assets to be deactivated for long periods of time.
And this is a huge issue. Every minute is crucial, so the longer an asset is switched off for a manual inspection to take place, the more money is lost. This can amount to millions of pounds each year.
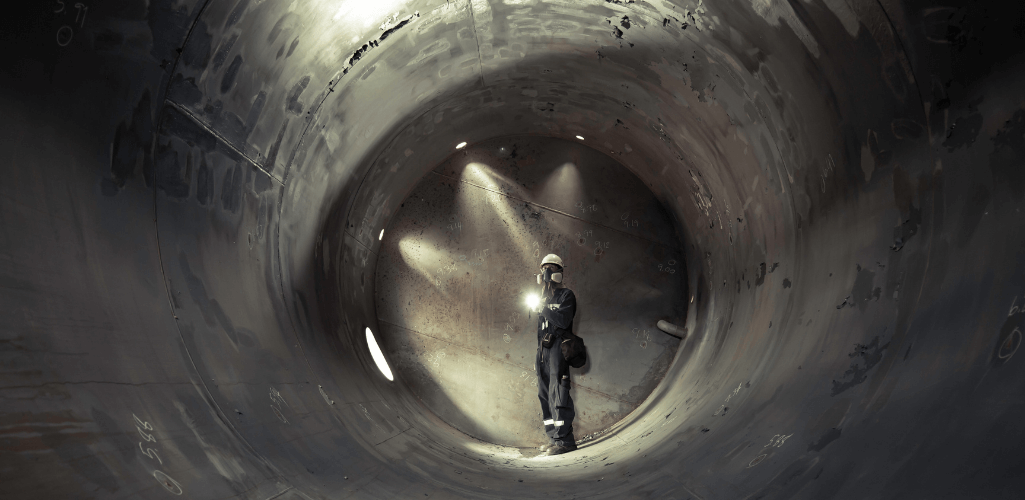
Benefits Of Using Drones For Confined Space Inspection
Drones provide an obvious solution to these issues, and in many cases, actually eradicate them.
In a nutshell, drones give inspectors full visual access to highly complex and hazardous spaces, ensuring a faster, safer, cost-effective and more accurate means of data collection.
Improved Safety
Using a drone for inspection dramatically increases health and safety.
Firstly, a drone reduces - or even removes - the need to send personnel into potentially hazardous environments or clambering up scaffolding to work from height.
If ground-based teams are required to enter a confined space, a drone can be sent in beforehand to analyse and assess the environment for threats or dangers.
Subsequently, this can eliminate the need to pay for and use scaffolding and rope access, as the drone can collect this data for you - all while teams remain safely away from the inspection area.
In many cases, drones can be operated beyond visual line of sight; especially useful for reaching hard-to-access areas or spaces.
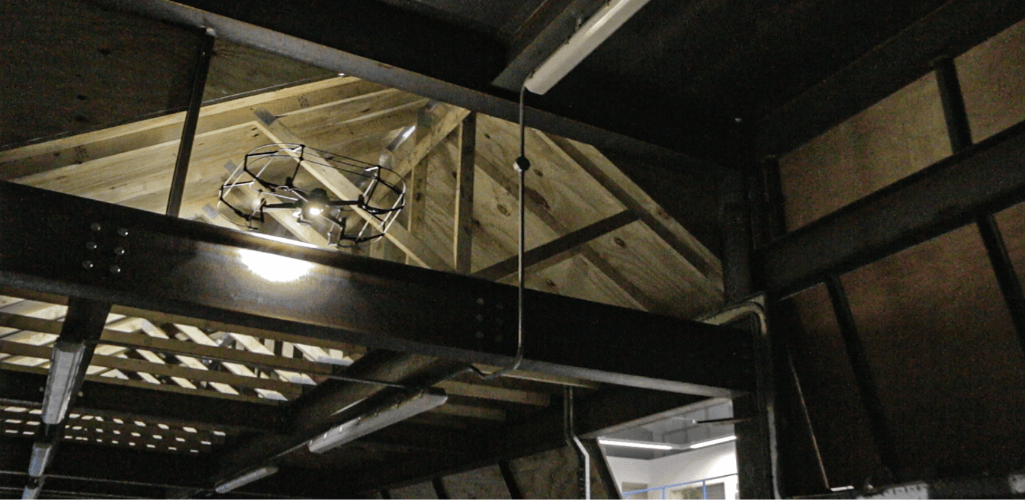
Quality of Data
Drones are incredibly reliable and efficient data collection tools, helping to quickly pinpoint asset anomalies.
One of the biggest benefits is that they can collect detailed aerial data in real time, using a suite of high-quality sensors and cameras.
The range of payloads available also ensure that drones are a versatile inspection tool, enabling inspectors to collect a wealth of information during a single flight, such as thermal and visual data.
Drones also have the ability to collect automated and repeatable data; especially useful for comparing the condition of an asset over a period of time.
The ease and cost-effectiveness of using a drone to capture this quality data also enables more regular inspections. These more frequent spot checks help teams build a more reliable picture of the condition of their assets and spot defects earlier, which can also result in huge savings further down the line.
Minimal Downtime
A drone can collect this quality data far more quickly than manual methods - resulting in minimal asset downtime.
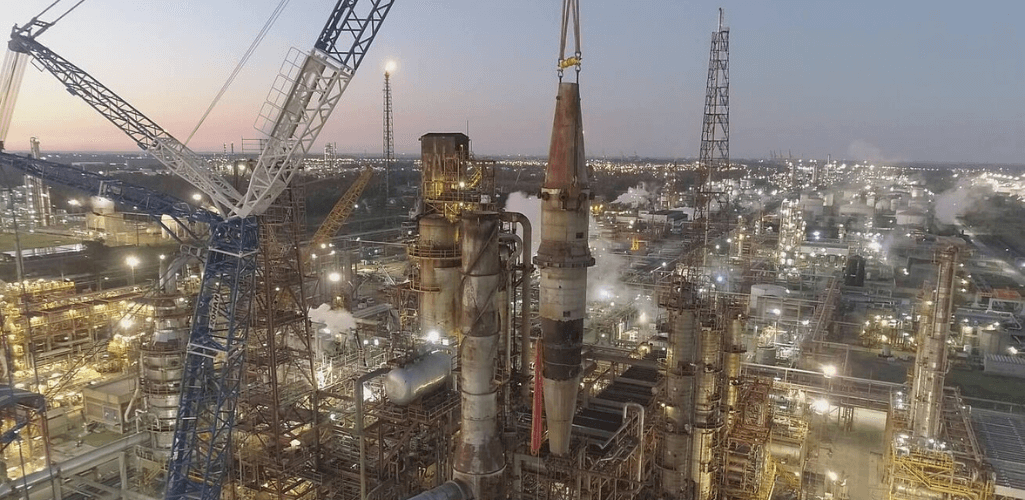
However, the big advantages of drones is that, in many cases, operations can actually continue to run while the aircraft conducts its critical inspections, resulting in maximised asset uptime and improved productivity.
Drone deployment can reduce the cost of inspection by more than 80% while drastically improving productivity through early defect detection and reduced down-time.
Reduced Costs
A drone ensures faster inspections, minimal downtime, less manpower, and a more accessible way of accessing the confined space - which all equates to more money saved.
Drones can also spot defects early, ensuring that issues can be resolved before they become worse, and more expensive.
Confined Space Inspections: Traditional Vs Drones In The Real World
There are numerous examples of drones being used to transform confined space inspections.
FSO Tank Inspection
Tanks are difficult assets to inspect.
Dark and tall, these types of inspections typically require humans to access the confined space with scaffolding, rope access or filling the tank with water and floating a dingy.
This method can take the best part of three days to inspect just one tank. The process is laborious: Open, purge, make safe, setup, inspect, close.
The complexity of the job requires a large crew - including rope-access team - breathing apparatus, on-hand tank rescue, and tank sentry.
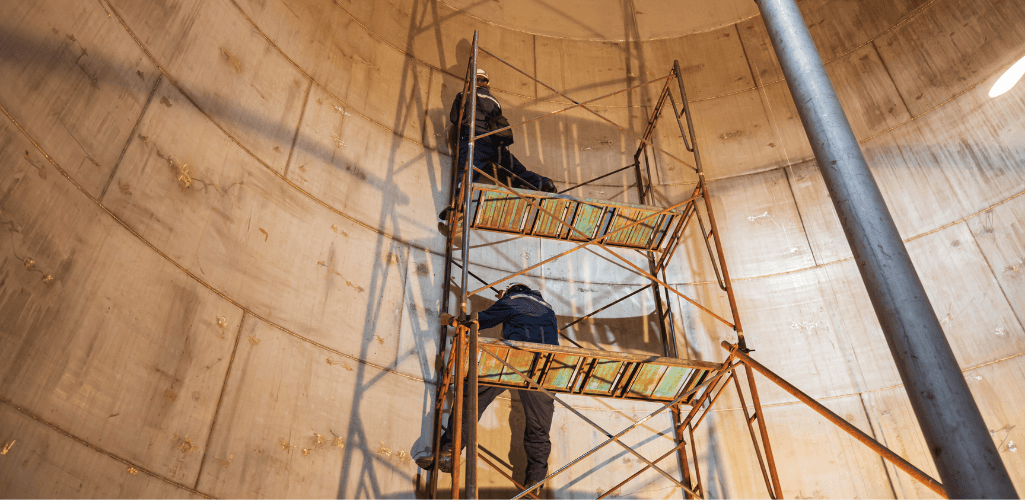
A drone changes all of this. Unmanned aircraft reduces the number of personnel to two: One inspector and a remote pilot; neither of whom have to enter the tank.
And the time to inspect a tank is drastically reduced - taking under two hours to inspect each one.
The result: 20 tanks inspected in nine days, instead of 60 - saving money and reducing risk.
Power Generation - Scrubber Inspection
In the energy industry, scrubbers clean the gases passing through the smokestack of a coal-burning power plant.
They are vital assets, but they are huge and uncompromising structures, which makes manual inspection extremely difficult.
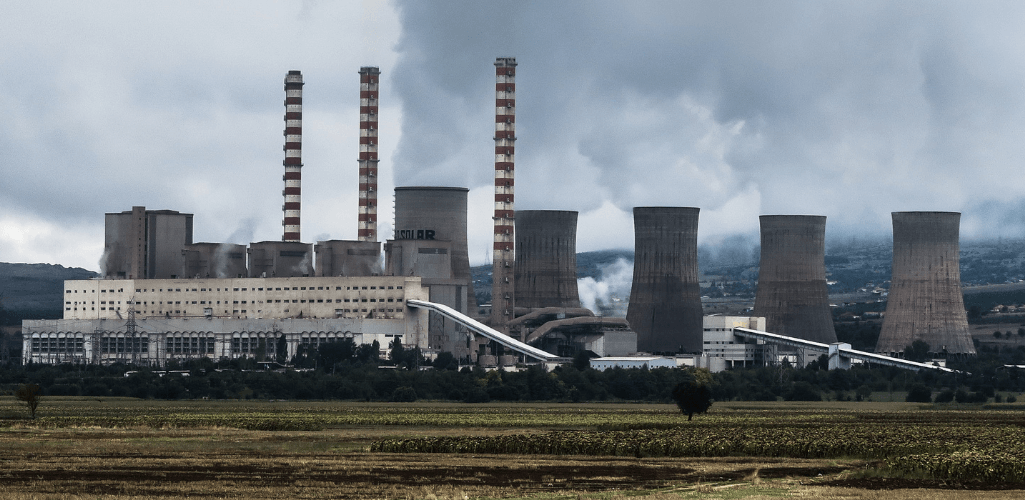
The traditional approach typically requires high-rise scaffolding - think 80 feet - to enable confined space entry.
Not only is this dangerous, but this method can be time-consuming, taking hundreds of hours.
But a drone empowers safer and quicker inspections. In fact, deploying a drone removes the need to build scaffolding and manually enter the confined space.
Energy company, TVA, utilised drones for scrubber inspections and realised a 98% saving in work hours, cutting the operation from 480 hours, to just 10!
Because drone inspections were cheaper, quicker and less complex, TVA was able to conduct more frequent checks, improving asset maintenance in the process.
Mining
Mines are hostile and dangerous environments, and some areas are inaccessible to humans and have traditionally required highly-expensive machinery to make this possible.
But drones offer the ideal solution - reaching these tough to access areas in a cost-effective way.
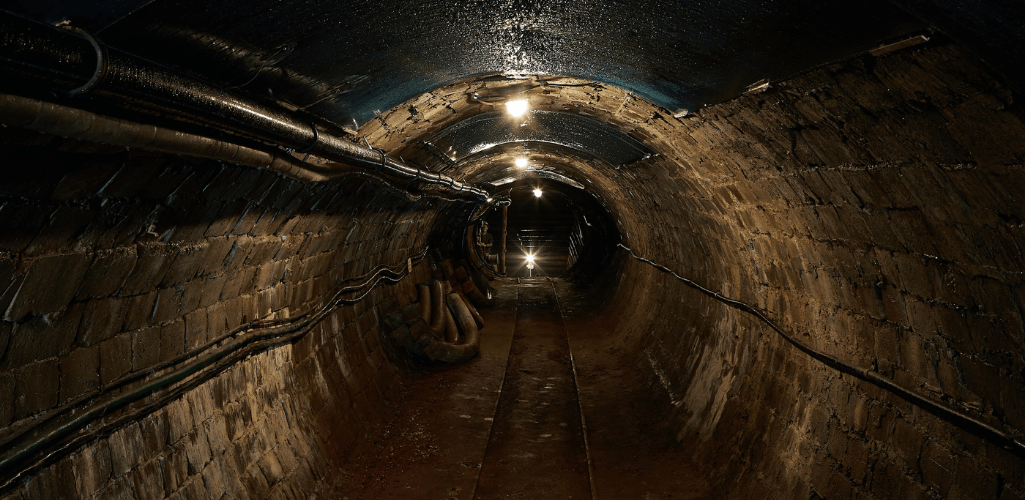
Drones are also ideal for inspecting mining assets, such as crushers, conveyor belts, stockpile feeders, and grinding mills.
In one example, international mining company, Barrick Gold, benefited from deploying a confined space drone at its Golden Sunlight Mine, in Montana, U.S.
The aircraft helped to find residual gold ore which had previously gone undiscovered.
The drone also enabled the company to collect visual data in areas of the mine that would have been impossible to gather otherwise.
Meanwhile, visual data of excavation sites enabled safety assessments previously impossible to collect, enabling unprecedented access within no-go-zones without exposing worker to hazards underground.
heliguy™ Mavic 2 Drone Cage
A protective cage on a confined space inspection drone is key to protecting the drone from collisions.
After all, there are challenges, such as navigating an aircraft beyond visual line of sight, operating within tight spaces, and often in dark areas.
To combat this, heliguy™ has designed a specialist cage for the Mavic 2 Series of drones.
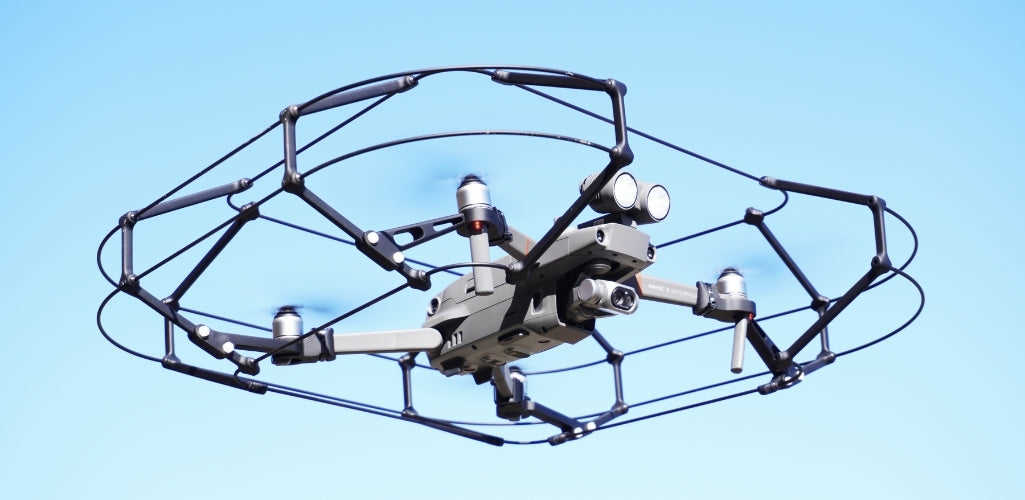
The frame - a low-cost entry to the caged drone market - provides 360° protection, is collision tolerant up to 3m/s, and provides unobscured camera views.
RELATED ARTICLE: The Evolution Of The Heliguy Drone Cage
The Mavic 2 Series is a versatile inspection solution, especially the Mavic 2 Enterprise Advanced which has upgraded specifications to enable users to capture quality thermal and visual data, including zoom.
Confined space inspection is often conducted within dark areas, and the cage provides enough room to house the bright spotlight accessory which can be integrated with the Mavic 2 Enterprise to illuminate low-light environments.
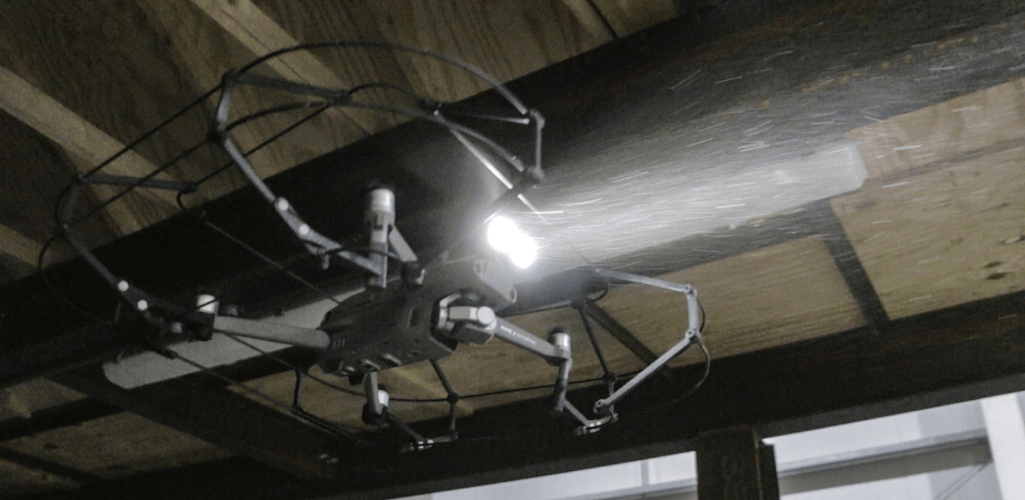
Click to purchase the Mavic 2 Drone cage.
Flybotix ASIO Caged Inspection Drone
Flybotix ASIO Caged Drone is a complete indoor inspection solution, engineered to help perform fast, efficient and safe inspections of your industrial assets.
This caged drone offers a collision-proof solution to collect accurate data remotely from difficult-to-reach and hard-to-access locations.
ASIO benefits from an impressive flight time of 24 minutes: Providing greater endurance than other internal inspection drones to obtain more information during a single mission.
A versatile platform, ASIO has 4K & thermal sensors and operators can view the data in real-time via a live stream. It minimises downtime, enables the early identification of defects, removes the need for scaffolding or rope access, and allows for more frequent inspections.
ASIO can be deployed to inspect nuclear facilities, power plants, lift shafts, underground tunnels and to check structural integrity following a fire, among other use cases.
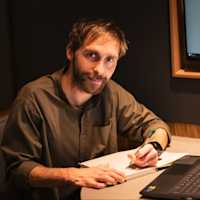
written by
James Willoughby
James joined heliguy™ in 2018 following a 13-year stint in print and online journalism, having worked on regional and weekly newspaper titles. He is responsible for spearheading heliguy™'s content strategy and social media delivery. James collaborates with DJI Enterprise's European marketing team to coordinate and produce case studies and helps organise events and webinars.